Key Word: Taili Plastic Machinery; Taili Plastic Machinery-Capacity Improving Expert; Efficient; Stable; Thick Wall Products The problem of shrinkage will easily occur to the thick wall injection molding products. For the technician, no matter how to increase the pressure or increase the injection time, they still can not solve this problem. Mr. Jiang of Jiangsu recently purchased several new molds and encountered such problems. After several days of continuous repair, the products still can’t meet the acceptance standard. Mr. Jiang told the technician that if the problem of shrinkage couldn’t be solved tomorrow, he didn’t need to come back to work the next day. The master in Mr. Jiang’s factory is an old friend of us. When he comes across such a difficult problem, he calls us to ask how to solve it. In fact, in order to solve this problem, it can be both easy and hard. The keys lie in:
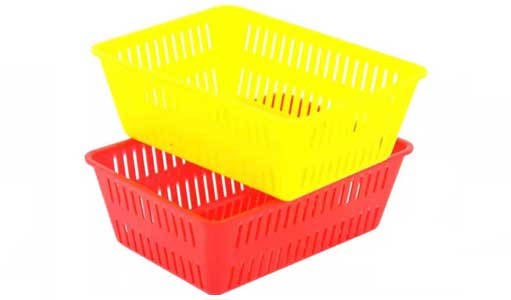
1. Judge the cause of raw materials and shrinkage Different raw materials applied lead to different causes of shrinkage, many technicians will confuse shrinkage with vacuum bubble. If we mistake the problem, we will inevitably go in the opposite direction. Jiang's factory mainly manufactures general household goods shell, thick wall, whose raw material is PP. In fact, for PP material, the shrinkage problem is easier to appear and more difficult to solve. The reason is that the thermal conductivity of PP material is very poor, the surface cooling speed is very fast, so it appears in the case that the surface has hardened but the interior is still fluid. 2. Reduce cooling time In view of the shrinkage problem caused by this cause, the method of shortening the cooling time is generally adopted. Many adjusting technicians think that since the shrinkage is uneven, the cooling time should be increased to make the product cool as soon as possible, so as to improve the surface accuracy. In fact, this idea is wrong. Only when the surface of the product is not completely hardened, take out the product and let the product shrink together can this problem be solved to the greatest extent. If the cooling time is reduced and the shrinkage of the product surface is not particularly improved, cold water can be used to assist cooling and shrinkage, and the shrinkage of general products will be greatly alleviated. 3. Increase injection speed For this kind of thick wall products, in the process of filling the mold cavity, we must improve the injection speed of the injection molding machine, so as to ensure that the fluid is not immediately closed after the injection. At the moment, the low-pressure holding process is used to ensure that the product is full and the shrinkage is reduced. This process requires highly for injection molding machine, not all machines can fulfill in this method. After adjusting the process according to our idea, Jiang's products were really optimized and the technician didn’t need to leave! Taili Plastic Machinery always keeps in mind that what a good injection molding machine factory should do is to help improving the capacity and boosting the profits, rather than offer the similar products the customers need. This is also what Taili Plastic Machinery keeps doing. Follow Taili Plastic Machinery and we will share more with you.
|