Key Word: Taili Plastic Machinery; Taili Plastic Machinery-Capacity Improving Expert; Efficient; Stable; Disposable Food Container Mold; Mold Test Disposable plastic food container generally refers to packaging products with wall thickness of about 0.35-0.5mm and produced by high-speed injection molding technology. Due to the thin wall thickness of product, the material and performance requirements of the mold are very high. So the price of the mold is higher than that of the general mold, and the test requirements are higher. Since Mr. Ma of Anhui started his business in 2019, he has more than 25 set of thin-wall fast injection molding machines to produce disposable food containers. Since the epidemic situation, due to the strong market demand, he has been adding injection molding machines, molds and personnel.
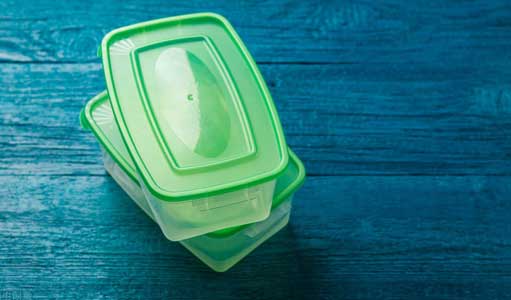
Recently, Mr. Ma has ordered 5 sets of molds, and the price of each set of molds is about 200000 yuan. Due to the busy production in the factory, he hopes Taili Plastic Machinery can help him test these molds. In fact, for disposable food container molds, the test method is very simple, with a total of three steps. 1. Water Connecting The first step to test the disposable food container mold is to connect the water, to see whether each cooling water flow smoothly, to observe whether each cooling nozzle is blocked, water volume is small or there exist any other problems. To the convenience, some mold manufacturers don't connect the water when they test the mold in their factories. Some waterways may be blocked by iron filings. Although this problem is easy to solve, it consumes a lot of time and energy. 2. Process debugging Generally, the hot runner temperature is set at about 240℃, and the barrel temperature is set at about 315 ℃. When the injection speed and pressure are the same, slowly increase the injection time. When one product is full but the others are not, stop increasing the injection speed. Turn to test the product weight of each mold at 20%, 50% and 70% of the time. If the deviation is large, the gate distribution is generally uneven, and the mold factory needs to make fine adjustment. 3. Shrinkage testing For thin-walled products, this step is the most critical and the easiest to be ignored. When the product has been able to start normal production, it is generally required to stop after half an hour of continuous production, and record the relevant parameters. Then remove the mold from the injection molding machine, place it for more than 24 hours, reinstall, and test with the previous production parameters. If the repeated parameters can’t be achieved, the material shrinkage of the mold doesn’t meet the standard. In the future production, the repeated accuracy of the product will be poor. After the above three steps of test, the mold of thin-walled products can be put into Mr. Ma‘s factory and start normal work without too much more debugging and correction. Taili Plastic Machinery always keeps in mind that what a good injection molding machine factory should do is to help improving the capacity and boosting the profits, rather than offer the similar products the customers need. This is also what Taili Plastic Machinery keeps doing. Follow Taili Plastic Machinery and we will share more with you. |