Key Word: Taili Plastic Machinery; Taili Plastic Machinery-Capacity Improving Expert; Efficient; Stable; PP Feeding Methods The runners of injection products are generally divided into cold runner and hot runner. The cold runner mold has the advantages of low cost and good material adaptability, which makes its market share far exceed that of hot runner mold. A few days ago, Taili Plastic Machinery made a return visit to Mr. Zhang's factory in Jinhua, and saw that his mechanic was stuck in adjusting the shrinkage process of plastic parts. We had a closer look into the cold runner and discovered that there were many secrets. Mr. Zhang's product is a household product, whose mold has 16 cavities. Obviously, there are many small bubbles at the tip of the runner. For PP material, this kind of small bubble is generally caused by shrinkage, that is, the mold holding pressure at the end of the injection molding machine can’t be smoothly transmitted, which results in the occurrence of bubbles. Thus, the shrinkage on the product surface will be very serious, which is exactly the problem troubles the adjusting technician most.
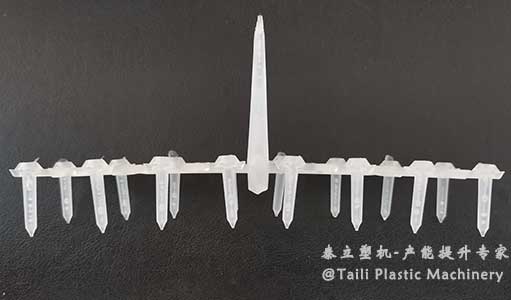
The ideas of adjusting shrinkage process of PP products go as follows: 1. Mold rubber inlet If conditions permit, expand the rubber inlet as far as possible. This is conducive to ensure that the injection pressure can be smoothly transmitted to the product in the third stage or during the pressure maintaining process, so as to prevent the shrinkage of the product. 2. Improve injection response speed We can reduce the injection speed at the head and increase the injection speed during mold filling to ensure that the internal fluid of the product is still flowing at the end of mold filling process, which can further increase the feeding force of the product. 3. Reduce material temperature Generally due to cost constraints, PP products rarely use mold temperature controlling machine. Therefore, under the condition that the requirements of product flexibility and physical strength are met, we should choose raw materials with high fluidity as far as possible and reduce the material temperature in the injection process, and keep the external surface and internal fluid of the product cooling at the same time, which is conducive to reducing the degree of shrinkage. After the above three steps, the big problem of Mr. Zhang's factory has been solved! Taili Plastic Machinery always keeps in mind that what a good injection molding machine factory should do is to help improving the capacity and boosting the profits, rather than offer the similar products the customers need. This is also what Taili Plastic Machinery keeps doing. Follow Taili Plastic Machinery and we will share more with you.
|