Key Word: Taili Plastic Machinery; Taili Plastic Machinery-Capacity Improving Expert; Efficient; Stable; 1250ml Round Plastic Food Container; Thin- Wall Container Solution For the boss of disposable food container, there are always several heartbreaking experiences that their products get returned. However, Mr. Sun of Jiangxi may be the only one who lost millions. The reason for the goods return is very simple. The food container is not well-sealed and suffer leaking, and even the lid cannot be covered. The dealer cannot sell all of them even after a year and wants to return all of the products, from which Mr. Sun suffers a lot. Mr. Sun of Jiangxi is not the first boss in the field of injection molded disposable food container whose product get rejected because of water leakage. But he is definitely the most tragic one. Because his products suffer not such a simple problem as water leakage as most of them can't be closed. Mr. Sun is also very confused that mold goes smooth in the factory test. How can it result in such high defection rate? When I first met Mr. Sun, he was troubled by these problems a lot. He did not dare to continue the production in the factory. He was afraid that the more he produce, the more he will lose. His friends recommended to him that Taili Plastic Machinery might do him a favor. Thus he came to Taili Plastic Machinery with his products for help. Mr. Sun's product is a 1250ml round plastic food container. After a close inspection, we found that the lid is hard to close. Though closed with a great effort, it will pop open immediately when filled with hot water or other hot stuff. So what does the problem lie? How can we solve this problem? Taili Plastic Machinery helped Mr. Sun solve this problem from the following three aspects.
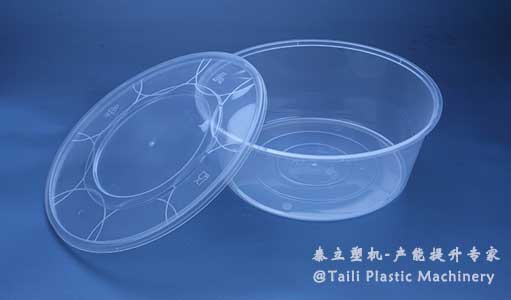
1. Check Raw Materials In face of such a big quality accident, the first thing we should investigate is the raw materials. Are the raw materials used to produce the bottom and lid of the same brand? At present, the common raw materials for disposable food container in the market are mainly Formosa Plastics 1450t, Lianhong and 9018. Generally, the raw materials for the bottom and lid are required to be of the same brand from the same manufacturer. PP materials produced by different manufacturers are of different shrinkage rates, which is easy to cause this problem. 2. Check Hot Mold Shrinkage Generally, the mold test in the injection molding machine factory or mold factory will last no more than half an hour. In this case, the mold is not fully heated, which is very different from the production situation in the customer's factory. It is necessary to measure the dimension change of the product under the condition that mold is fully heated. The measurement must be carried out 24 hours after demoulding. Otherwise, because of the change of shrinkage rate, it may lead to the situation that the food container can't be covered after a period of time though it is very good at first. 3. Check Injection Temperature And Process Conditions For this kind of high-precision mold, injection molding process has a great influence on product shrinkage. It is necessary to check whether the product process is consistent and whether there are any problems in the production sequence during the production process. Then adjust and improve the injection molding process conditions. Mr. Sun checked and found that none of the three problems was satisfied. He at first changed the raw materials and checked the shrinkage rate in the case that the moldās fully heated. At last, the product turns to be of no problems any more. Taili Plastic Machinery always keeps in mind that what a good injection molding machine factory should do is to help improving the capacity and boosting the profits, rather than offer the similar products the customers need. This is also what Taili Plastic Machinery keeps doing. Follow Taili Plastic Machinery and we will share more with you.
|