Key Word: Taili Plastic Machinery; Taili Plastic Machinery-Capacity Improving Expert; Efficient; Stable; Disposable tableware For the thin-wall high-speed injection molding machine, the stability and high speed of the product are the most important parameters. The thin wall high-speed injection molding machine is mostly used to produce disposable tableware, such as fast food box, knife, fork, spoon, cup, etc. A few days ago, Mr. Liu of Yiwu called me and said that the injection molding machine in their factory was amazing. At 6 a.m. every day, there occurred problems such as lack of materials and flash. If the parameters are changed at this time, the product won¡¯t be stable until nearly half an hour to an hour of production later; If the parameters are not changed, it will take about half an hour to restore stability.
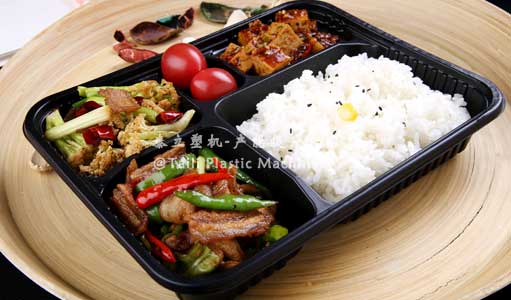
In fact, Taili Plastic Machinery has encountered many similar problems before, and the main solutions are as follows: 1. Ask the night shift master about the machine adjustment process Usually, the night shift master will deliberately slow down the production cycle of the injection molding machine due to the work intensity. In the case of large temperature difference between day and night in winter in South China, due to the slow cycle time at night, the cooling water is cooler and the water temperature rises faster after sunrise, which is easy to affect the unstable product quality to a certain extent. 2. Check the expansion coefficient of the die This kind of situation mostly occurs to the machine with large mold plate, such as those for the mold with 8 or 16 cavities. Therefore, in the case of large temperature difference between cold and hot, shrinkage and expansion will be easily caused respectively by supercooling and overheating. This factor will affect the transient instability of the product, which can be solved by restoring the injection molding machine to the thermal equilibrium state. 3. Check the chiller In the case that the mold casting area is not large and the mold with 4 or 2 cavities, there¡¯s generally no need to use the chiller. Because in the summer in the south, due to the extremely high temperature, the high temperature of the cold water and injection of the chiller is generally above 315 ¡æ, which will form quenching effect on the mold. When the mold is large, such as with 8 or 16 cavities, the chiller can be used to reduce the product error caused by mold shrinkage. After checking the night shift master, Mr. Liu finally solved the problem. Taili Plastic Machinery always keeps in mind that what a good injection molding machine factory should do is to help improving the capacity and boosting the profits, rather than offer the similar products the customers need. This is also what Taili Plastic Machinery keeps doing. Follow Taili Plastic Machinery and we will share more with you.
|