Key Word: Taili Plastic Machinery; Taili Plastic Machinery-Capacity Improving Expert; PC power strip£»Silver streaks; Bubbles; Efficient; Stable PC, Polycarbonate is a very widely-used engineering plastic and it is commonly used in the manufacture of power strip. When I first entered the injection molding industry, the processing adjustment and parameters of PC materials confused me a lot. The biggest problem troubling me was the appearance of silver streaks and bubbles in the PC products. Mr Bian, from Ningbo Cixi, always came to us for the bubbles appearing on the power strip (PC) he produced. I shared with him the unique secret tips, that I have studied and experimented through the years, for dealing with silver streaks and bubbles in PC manufacture of PC products.
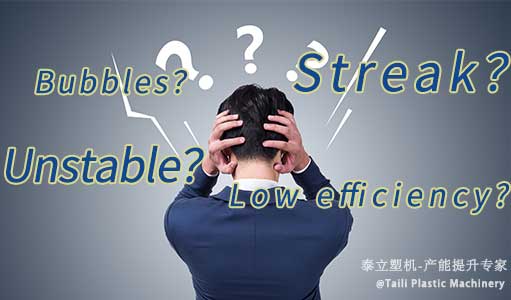
To solve this problem, we must first clarify the reasons for these bubbles appearing on the PC products. The reasons for these problems are generally due to the gas interference during the filling process. Whether it is silver streaks, air bubbles or vacuum bubbles, it is generally caused by the interaction of moisture, air, decomposition gas and dissolved gas. To solve these problems, you can investigate the causes of these gases one by one. 1. Moisture PC (polycarbonate) is extremely sensitive to moisture, and generally the water vapor content is required not to exceed 0.02% during its injection molding process. For Bian's products, I first asked him to check whether the PC material was fully dried according to the material requirements before injection molding. The PC material drying requirement is generally 120 degrees and it takes about 4 hours to dry. Obviously, as a veteran in this industry, Bian didn¡¯t make any mistake in this regard. 2. Solvent Gas The generation of solvent gas is mainly related to the specific process process. Based on Bian's understanding of PC, he did not add too many additives. Thus, the cause of solvent gas can also be ruled out. 3. Decomposition Gas PC materials are easily decomposed due to material temperature and shear force stroke, which generates decomposition gas. Bian¡¯s normal injection temperature was 240 degrees, which didn¡¯t exceed the decomposition temperature of PC. At the same time, we checked the injection speed, pressure, injection back pressure and other parameters concerned. There turned to be of no problems. Therefore, PC material decomposition due to material temperature and shear force can also be ruled out. 4. Air There are generally two sources of air: one is that the material inherently contains air in during the storage process, and the other is that the mold and machine process are not properly coordinated. The PC material quickly flows into the mold cavity, making the air in the mold cavity impossible to exclude. Vortex is formed, thereby bubbles form on the surface of the product. For air bubbles due to the storage process, we can make the machine inject to the air and see if there are any bubbles in the injected material. If yes, the back pressure and speed of the storage material can be adjusted to alleviate this situation. The trapped gas of the product can be eliminated by adjusting the mold to strengthen the exhaust and reducing the injection rate inside the mold (except the water outlet).
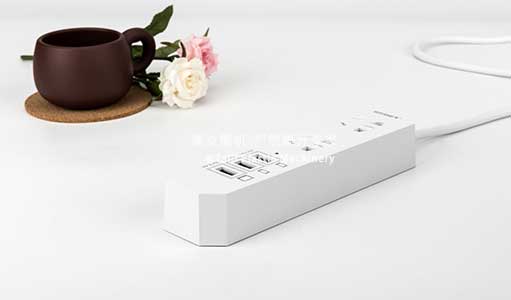
After a series of investigations, it is obvious that Bian¡¯s problem came from the improper cooperation between the mold and the machine process. After appropriate reduce of the die speed, the product quality was significantly improved. Taili Plastic Machinery has been helping customers to solve the problems and improve profit margins. It is the rule we always remember: selling machines is only the beginning of cooperation. |